About Membrane Switches
A membrane switch is a momentary closure device used with a normally open circuit. They are called membrane switches because they are made up of flexible graphic and internal layers (or membranes) over a circuit printed on PET or etched on polyimide.
The layered nature of membrane switches allows a great deal of freedom for engineers to design and implement a very precise customer experience. Because of this flexibility, these user interfaces are used across a wide range of industries, including medical, consumer electronics, military/DoD, and aerospace.
There are many parameters to consider in membrane switch design including the graphics, overlays, adhesives, and use cases.
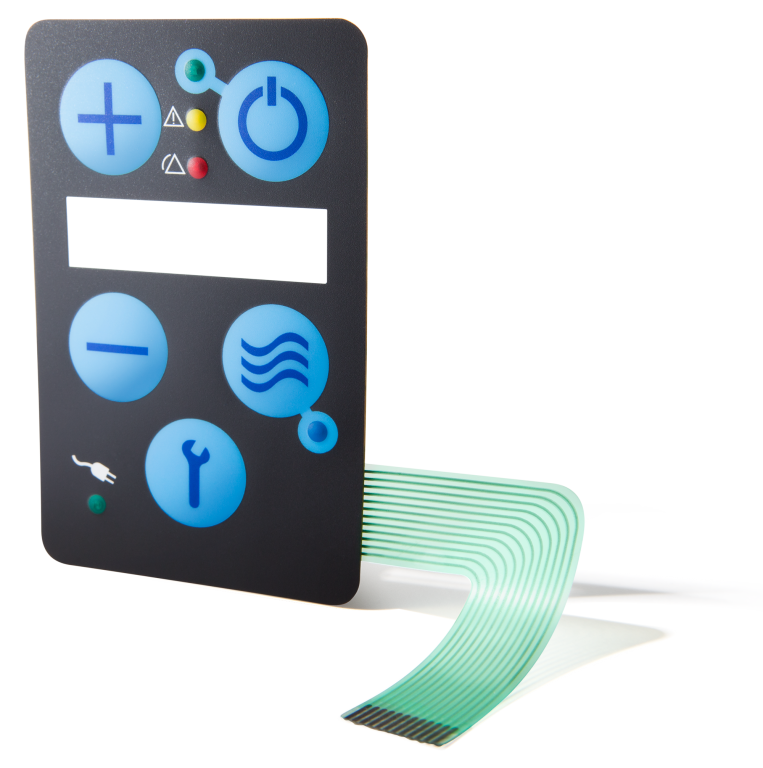
Membrane Switch Components and Terms
There are many parameters to consider in the development of custom membrane switches, including the design, overlays, adhesives, and use cases. They can vary a great deal from simple to very complex. The components of a membrane switch will vary with complexity, but all contain some combination of the following:
Graphic Overlays
The overlay is the top layer of a membrane switch and is the interface between the user and the machine. Two of the most important issues to consider with graphic overlays are durability and environmental concerns. Graphic overlays can be made of polycarbonate, polyester, or acrylics, and your choice of material will depend on the desired level of durability and whether it needs to be protected against scratches, chemical abrasions, extreme temperatures, or actuation. For good tactile feedback in a switch, choose an overlay thickness between .006 and .010. This range will offer the durability to meet your requirements, with the sensitivity to provide a quality tactile effect.
Adhesive
The adhesive is important in two layers of membrane switches; it combines the switch to the graphic overlay and will bind the entire assembly to your product. There are numerous differences in adhesives; selecting the proper adhesive for application requires consideration of environmental, surface, appearance and other performance requirements.
Embossing
There are three basic styles of embossing; pillow, rim, and poly-dome. Depending on shape and size, logos and multi-level shapes can be embossed. Buttons can also be embossed for added tactile definition.
Circuits
Circuits can be printed using silver conductive ink, etched copper flex or printed circuit boards (PCBa’s).
Surface Mount Devices
Membrane switches can be designed with almost any SMT component embedded if needed, resistors, light sensors, and any low surface mount component if required.
Touchscreens
The integration of touchscreens into membrane switches offers a compact and streamlined user interface. The touchscreen component is precisely aligned beneath the membrane switch, ensuring a seamless and cohesive appearance.
Shielding
Proper shielding is necessary to meet ESD, EMI or RFI requirements.
Tactile and Non-Tactile
Membrane switches can be designed as tactile or non-tactile to achieve the desired product requirements.
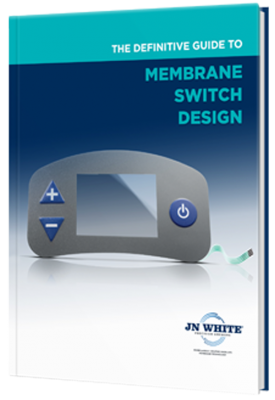
Design Your Own Membrane Switch
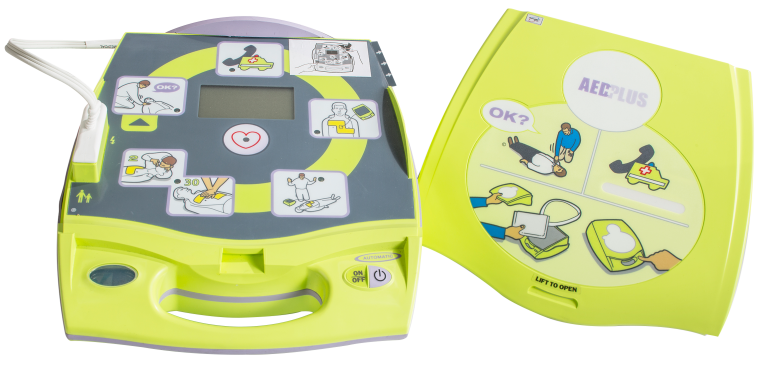
Constructions
Simple Membrane Switch Constructions
This three-layer switch, comprised of graphic overlay, a circuit spacer, and a screen-printed silver ink circuit, is the simplest type of membrane switch. Because they tend to be the least expensive option, they are often implemented as a cost-cutting measure in the overall design.
Considerations for Simple Membrane Switch Constructions
Tactile vs Non-Tactile Feedback
Tactile feedback refers to the feel you experience when you push a button. By using different materials and sizes for these buttons, you can vary the actuation force required to activate the switch.
Tactile Switch with Silver Circuitry
Tactile switches incorporate a metal dome or a polydome into the membrane assembly to achieve a desired tactile (and sometimes audible) response. By using different materials and sizes for these domes, you can vary the actuation force required to activate the switch. Read About Tactile Switches >
Non-Tactile Switch with Silver Circuitry
Since there is no tactile feel when these circuits are actuated, there is often a sound or light component put in place to indicate activation. Depending on the device and the design, electronic shielding techniques may also need to be incorporated. Read About Non-Tactile Switches >
Complex Membrane Switch Constructions
Complex user interface designs often need more components than their simple switch counterparts, usually resulting in more layers. Multi-layered switches may include some form of ESD, EMI, or RFD shielding, embedded components like LED’s, resistors, light sensors and even programmable chips. To accommodate these more robust designs we are often using copper flex or PCB’s for the circuit layer. As a result the electronic options are virtually limitless.
Additional Considerations for Complex Membrane Switch Constructions
Copper Flex Membrane Switches
Unlike screen-printed silver, copper flex circuits are manufactured by laminating copper to an underlying substrate, and then etching that substrate in a way that leaves specific conductive traces, resulting in a more flexible, durable, and precise circuit that compounds can be soldered to. Read About Copper Flex Circuits >
Printed Circuit Boards (PCB’s)
Some user interfaces require higher-density, more miniature components. In these situations, printed circuit boards (PCB’s) and printed circuit board assemblies (PCBa’s) are often brought into play. Read About Printed Circuit Boards >
LED Backlighting Options
Designing the right backlighting technology into a switch assembly can help deliver a superior user experience. A wide variety of backlighting options are available, allowing engineers to precisely manage light quality, color, intensity, and coverage, so it is important that your selected switch manufacturer understands the advantages and disadvantages of these different techniques and how to properly incorporate them into a design. Read About Backlighting Technology >
Dead Front Display
When a clean aesthetic and emphasizing certain icons is important, dead front displays are utilized. Dead fronting is a term used to describe an icon that is typically hidden from view but is visible under certain circumstances. The dead front icon must be transparent and allow light to shine through, therefore illuminating the icon, while the surrounding overlay must remain opaque and undisturbed by the backlight. Read About Dead Front Displays >
Touchscreen Integration
Incorporating touchscreens into complex membrane switches requires a delicate balance between functionality, usability, and aesthetics. At JN White®, we excel in seamlessly integrating different types of touchscreens into your interface design. We understand the importance of selecting the right touchscreen technology and properly incorporating it into the overall assembly. Read About Touchscreens >
Visual Design Considerations
Digital printing, color management, inks, finishes, and embossing all dramatically enhance the look and function of a switch. At JN White®, we have a computerized color formulation system to achieve consistent results from piece to piece, as well as ones that can color match to the Pantone Matching System, Federal Standard Guide, a color swatch, or to your bezel. Read About Membrane Switch Color >
Environmental Considerations
Switches need to be reliable for years, all the while being used on a daily or even hourly basis. This requires an active and purposeful design for lifetime actuation. When building a switch, it’s important to consider the types of durability needed, material selection, and whether it needs to be weather sealed. Read About Environmental Considerations >
Pitches of Conductor Pads on Membrane Switches
How To Install a Membrane Switch
Our resident switch expert, Ken Boss, shows you how to install a membrane switch onto your products. The full instructions can be seen below.
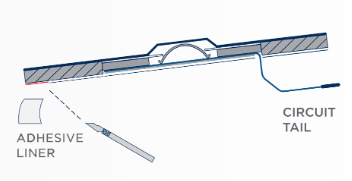
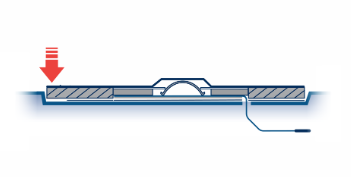
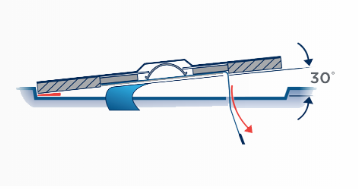
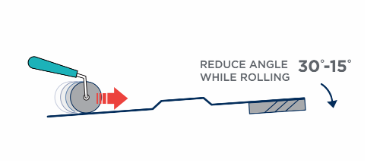
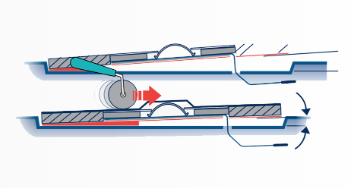
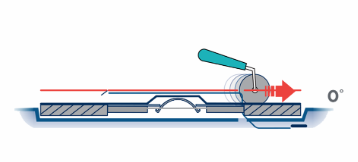
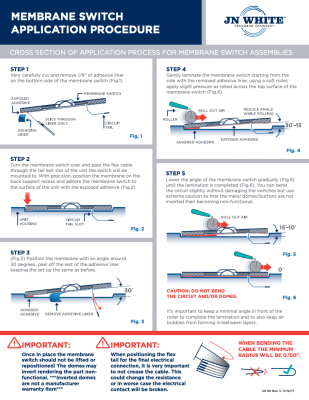
View Membrane Switch Application Procedure as PDF
Membrane Switch Installation Dos and Don'ts
Ken Boss explains what to stay away from when installing your switches. Take heed of his advice to keep your switch working properly after install.
Why JN White®?
At JN White®, we have developed deep expertise and experience as a membrane switch manufacturer – an expertise that our customers have come to rely on when they are trying to design and implement specific user interface objectives. Integrating features like those noted on this page, we can expertly manufacture the most challenging panel assembly applications in the most demanding environments, including medical, electronic, military/DoD, and industrial markets.
Because there are so many parameters to consider in the design of membrane switches (including the graphics, overlays, adhesives, and use cases), we often consult with customer engineering teams early in their development process to ensure feasibility of their designs and optimal outcomes.
Check Out Our New Power Pack Samples!
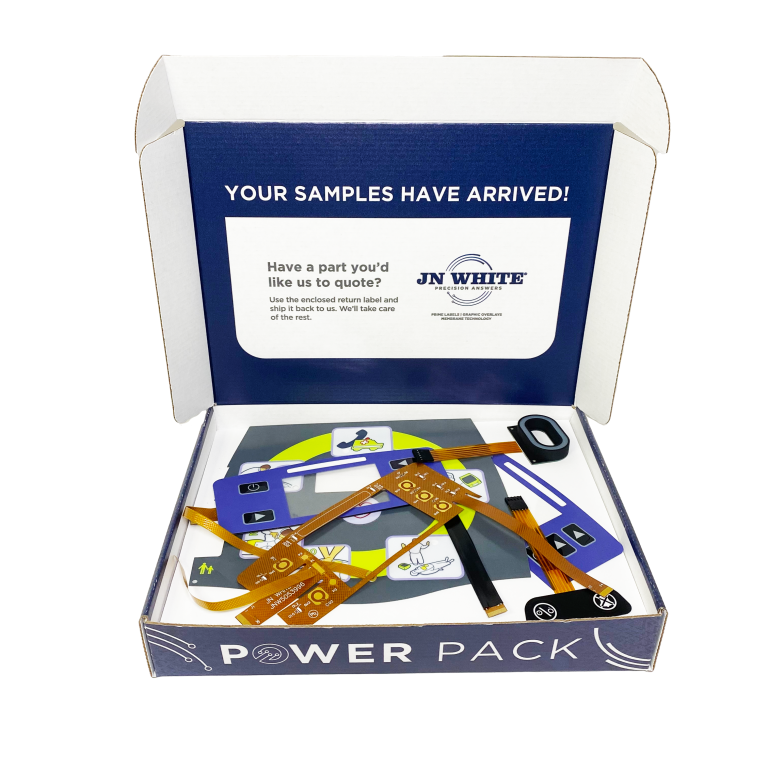
We have compiled a variety of our most versatile membrane switches and unique samples that you can feel and interact with, free of charge. See first-hand the quality, function and durability these highly customizable switches provide users. Request a Power Pack today!