What is Electrostatic Discharge?
As a body comes into contact with different materials, it is charged with negative electrons. When those electrons come into contact with grounded conductive objects such as those found in membrane switches, they create a quick discharge of energy, or electrostatic discharge (ESD). For a fraction of a nanosecond, this discharge can reach up to 15,000 volts (15kV) with a current of up to 30 amperes.
When a user manipulates a membrane switch, the discharge passes from the user to the switch and the sensitive electronic components inside, potentially wreaking havoc on the delicate ecosystem of wires and circuits. Even though a fraction of a nanosecond is a very short amount of time, the levels of ESD are extremely high, and it only takes a small portion of this brief discharge to cause a circuit to malfunction, or other forms of serious damage to electronics. It is critical that membrane switches be designed to prevent the ESD arc from reaching their sensitive circuitry and components.
Shield Your Membrane Switch from ESD
An ESD shield is typically a layer, or multiple layers of material that protects the sensitive electronic systems of your membrane switch from the discharge.
JN White® has found there are two options that work best for proper ESD shielding.
1. A screen-printed grid pattern of conductive silver ink
This layer can be grounded to a trace on the interface panel and then routed to a grounded plane on the motherboard to carry the static charge away from any nearby conductive components. A separate tail for the shielding layer can also be designed to connect to the housing or another mechanical piece already grounded.
2. Use of full conductive laminates, tapes, and foils inside the product
These provide a higher level of dissipative properties, but they can also be more expensive. To determine which technique should be used, consider the absorptive properties of the overlay materials.
In both of these applications, the key is to manage the dual nature of the protective layer. On the interface side, the conductive layer is on top to catch the static. Then a laminate insulating layer is placed underneath to protect the components.
Common Materials Used in ESD Shielding
There are a number of materials you can use to shield your electronic components from ESD.
Polyester
Polyester is a very common and cost-effective option. It is a very thin layer right behind the graphic overlay. Once the silver screen-printed grid pattern comes into contact with ESD, it guides the discharge to the chassis ground.
Aluminum Single Side Coated Foil
A thin aluminum layer, around 3-5 ml, can also be used to transfer the discharge away from the electrical components. The conductive side lays right side up and guides the ESD through a ground chassis point.
Conductive Copper Mesh Fabric
Conductive copper mesh fabric is a very high quality option only used in special applications due to its more expensive price tag. It is frequently used in communication and military units. A single layer of copper mesh fabric will also protect components from electromagnetic interference (EMI) and radio frequency interference (RFI).
Indium Tin Oxide (ITO)
Indium Tin Oxide (ITO) is a clear, electrical conductive transparent, plastic polyester material that is used when a display needs to be shielded from electrostatic discharge. It is difficult to produce and can be more costly, but will fully protect the display area from ESD, EMI, and RFI.
How ESD Shielding Works for Membrane Switches
ESD can reach switch circuitry in two ways: it can punch directly through the layers above the circuitry, or it can flash around and between the layers that protect the circuitry.
On the top of the membrane switch interface, you can incorporate a few dielectric barrier layers like a graphic overlay (made of polyester and 0.006”-0.007” thick), top pressure sensitive adhesive, and a dome retainer (made of polyester and 3-5 mil thick) that will aid in shielding. Usually, this is an efficient ESD barrier that can withstand 2kV / 0.001” thickness.
In order for ESD to punch through top layers, it would have to have a voltage higher than the material’s dielectric strength, measured in volts (V) per unit thickness. If the insulating material for the plastic overlay material is 0.007” thick and has a dielectric strength of 2 kV per mil, then the point at which ESD breaks down has to be more than 14 kV.
We follow specific best practices, like adding a gasket all around the switch or moving the traces as far away as possible from the edge of the keypad, to minimize the ESD arc that reaches the circuitry by flashing around and between the membrane switch layers. If edge distance is a problem, an efficient, low-cost option is to allow the first and last contacts of the connector to make contact with an earth-grounded loop on the edge of the circuit layer away from any circuit traces.
When to use ESD Shielding
Not all products require ESD shielding. Since our work with shielding requirements typically occurs at the interface level, where human beings (who are a great source of ESD current arc) directly interact with a product, we’ve developed a step logic that helps us determine when shielding is necessary.
- If the product is going into an environment where there is a high risk of a static charge being applied by the user when pressing the buttons
- If they have a customer or regulatory requirement that drives ESD protection to a certain level
- If static sensitive components are near the surface of the keypad inside the unit
While this logic is specific to membrane switches and the other kinds of interfaces we typically work with, it can be adapted and applied to many other applications.
Testing ESD Shielding
The effectiveness of ESD shielding can be tested using two methods prescribed by ASTM test method F1812: one for measuring contact discharge, and the other for measuring air-gap discharge.
Both methods require some form of shielding that is connected to earth ground during testing. The contact discharge method measures shielding when the discharge tip of a special ESD gun is in direct contact with the keypad. The air-gap method measures shielding when the gun is discharged at a specified distance above the keypad.
For specific applications, the customer must provide performance criteria for the switch so we can accurately evaluate ESD protection level, including the following:
- interface application type
- mounting conditions for the switch assembly (details about housing, connections, etc.)
- discharge test method to employ if applicable (contact and/or air-gap)
- ESD voltage protection required (kV)
Electrostatic Discharge Shielding Application
Check Out Our New Power Pack Samples!
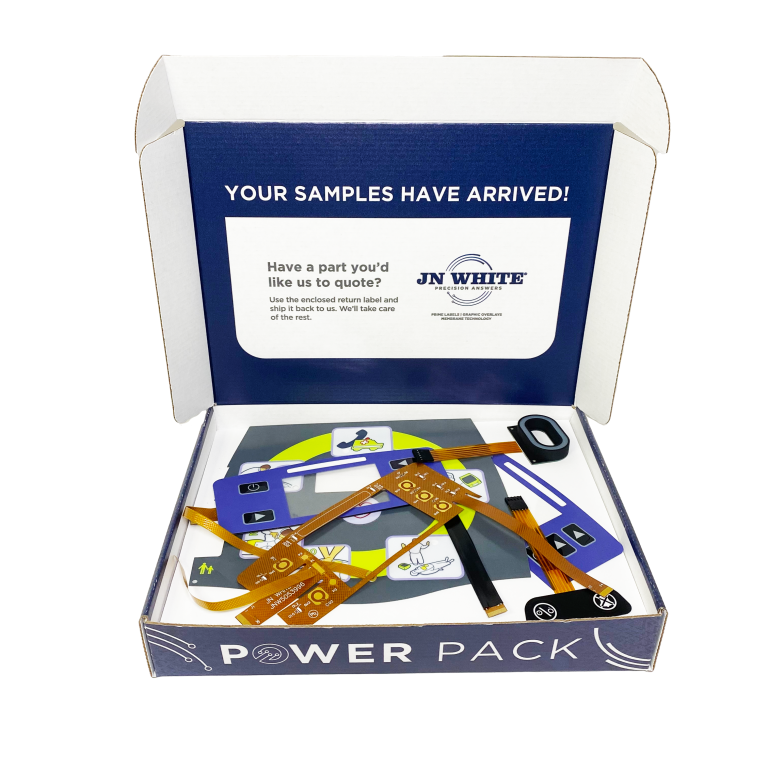
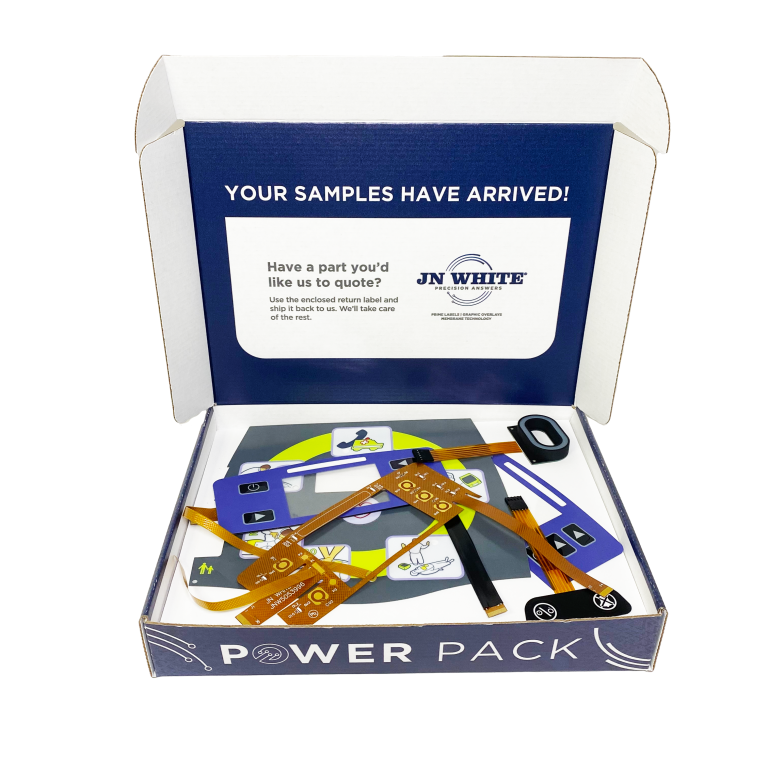
We have compiled a variety of our most versatile membrane switches and unique samples that you can feel and interact with, free of charge. See first-hand the quality, function and durability these highly customizable switches provide users. Request a Power Pack today!