Tactile vs. Non-tactile Membrane Switches: Which Is Right for Your Product?
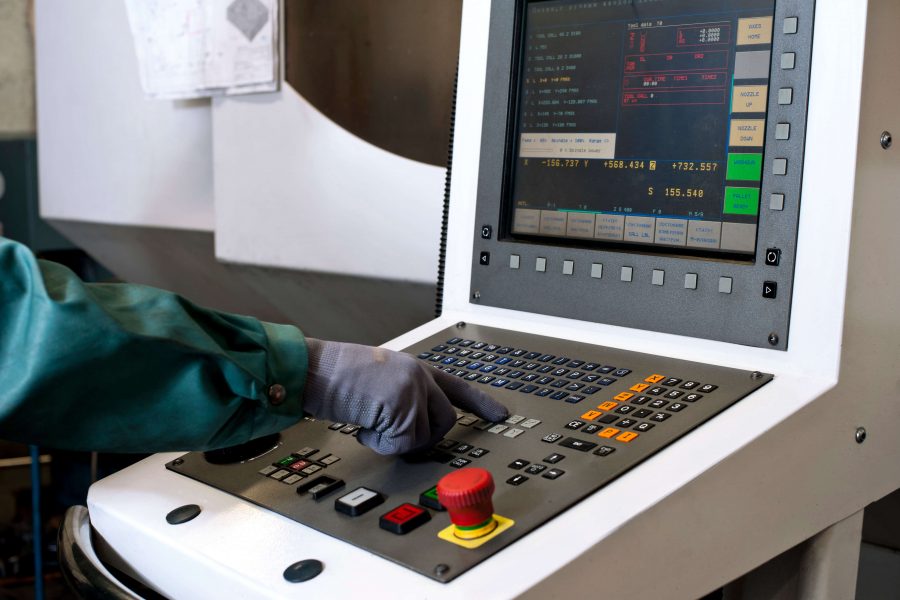
Membrane switches are affordable, customizable, and highly functional user interface components. Custom built for a wide array of products throughout the consumer electronics, medical, and industrial markets, membrane switches are durable and reliable tools that allow users to easily interact with a device.
Essentially functioning as a switch that controls when a circuit is open or closed, membrane switches tend to provide the same functionality as physical knobs, dials, or buttons. But because membrane switches can be used in concert with polycarbonate, acrylic, or other durable graphic overlays, they act as a resilient, reliable method of product interaction that’s easy to maintain in even the harshest of environments.
What are the different types of membrane switches?
There are two key types of membrane switches: tactile and non-tactile. While each provides the same essential functionality for a user to control a specific interaction with a device, tactile and non-tactile interactions offer noticeably different user experiences:
- Tactile membrane switches provide a physical, tactile response when pressed. When interacting with a tactile switch, a user typically presses on a metal or plastic dome beneath the graphic overlay, providing an unmistakable feeling that a “button” is being pressed. Tactile switches can be fitted to a wide variety of shapes and sizes and require different amounts of actuation force in order to fulfill particular functions.
- Non-tactile membrane switches do not provide a physical, tactile response when pressed. Because tactile feedback cannot be felt, activating a non-tactile switch typically triggers a sound or light to indicate that the function has been performed. Because additional layers intended to provide a tactile response are not required by non-tactile membrane switches, these devices tend to be the least expensive option for product interaction.
Choosing between a tactile and non-tactile membrane switch depends on the specific use case, interaction preference, and the overall cost of a product’s components.
What are the pros and cons of tactile membrane switches?
In applications where eliciting physical feedback is essential for the product design, tactile membrane switches are the ideal solution. Because tactile membrane switches are highly customizable and responsive to different amounts of force, providing clear feedback from a user interaction can deliver a much more positive user experience.
Tactile switches, however, require a greater number of physical components and can cost more to design and assemble. In instances in which reliability and price concerns outweigh the user interface, tactile feedback may prove to be an expensive luxury.
What are the pros and cons of non-tactile membrane switches?
Non-tactile membrane switches are far less complex to manufacture. Because they have fewer components, they can be manufactured at the lowest possible price. However, they can also require a different type of feedback to inform the user that a device has been interacted with, such as playing a tone or emitting light, so additional costs and complexities may be involved.
Because non-tactile membrane switches do not produce a physical response, users may experience a less-than-satisfying experience after pressing a button. In instances where tactile feedback is not important, non-tactile membrane switches can nevertheless provide a cost-effective method of user interaction.
When should a company choose a tactile membrane switch or a non-tactile membrane switch?
Determining whether a tactile switch or non-tactile switch is best for a specific product can depend entirely on the particular use case.
Generally speaking, tactile switches are ideal for circumstances in which it’s important for a user to feel as if they have pressed a physical working button, such as on medical equipment or in a factory setting. Non-tactile switches are good choices for companies looking to save money on manufacturing costs and in instances where physical feedback isn’t necessary.
Since 1960, JN White® has manufactured critical technology components to help companies bring their products to life. To determine whether a tactile or non-tactile switch is the right fit for your product, contact JN White today !
More from Ken
In today’s rapidly evolving technological environment, the need for innovative and dependable membrane switch prototypes is continuously increasing. As a leading membrane switch manufacturer, JN White excels in crafting custom membrane switch prototypes that not only meet your specific design…
Projected Capacitive (PCAP) touch technology has revolutionized modern touchscreens, providing highly responsive, durable, and intuitive user experiences. From smartphones to industrial control panels, PCAP touchscreens are now the gold standard for applications requiring precision and reliability. At JN White, we…
Understanding the Importance of ESD Shielding Electrostatic Discharge (ESD) is a critical concern in electronic device design, particularly for sensitive components like membrane switches. Without proper ESD protection, these switches can suffer from performance issues, reduced lifespan, or even total failure….