Precision Cut Components
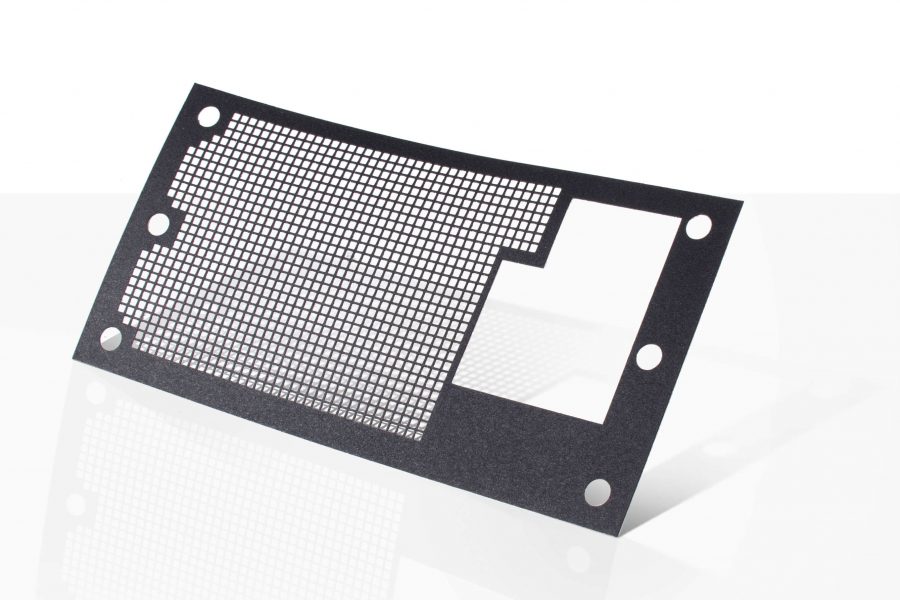
Although commonly referred to as die cuts, die cutting is just one process utilized to create precision cut components. Die cutting is a versatile and widely used fabrication process that involves specialized machines and tools to convert stock material into custom shapes and designs. These components are created by cutting non-printed materials into various shapes to address different issues such as vibration damping, EMI shielding, electrical insulation, bonding, gasketing, and sealing.
Precision cut components have a wide range of applications and are commonly used to produce elements for different industries, including automotive, medical, and electronics.
These components are customized to meet specific requirements and are created using a variety of materials such as foams, rubbers, pressure-sensitive adhesives, polycarbonate, acrylic, and foils. They offer several benefits, including improved product performance, increased product lifespan, reduced product weight, and enhanced design flexibility.
Let us first take a look at the common terms used to describe different types of cuts, before jumping into the cutting systems implemented to produce them.
Cutting Operation Capabilities
The die cutting process offers several different cutting operation capabilities, including:
Through Cut– Through cutting is the process in which the cut goes all the way through the material.
Kiss Cut– A kiss cut is the process in which the cut goes through the primary material, but doesn’t penetrate the adhesive or backing liner. This allows for a larger backing/liner that remains after the cut, which is easier to remove in the manufacturing process.
Perforating– A perforation is a cut in a piece of material that makes it easy to tear, like the neat row of perforations that allows you to rip a sheet out of your notebook cleanly.
Scoring– Scoring refers to the process of making a crease in a material so it will fold easier. Basically, a score is a ridge that is indented into the material where the fold line will occur.
Precision Cutting Systems
There are different types of die cutting processes available, including flatbed die cutting, Preco automated die cutting, laser digital cutting, and Zund precision blade digital cutting systems. JN White utilizes them all and each has its own advantages and disadvantages. The type of die cutting process most suitable for a given application depends on factors such as the materials being converted, part size, desired tolerances, costs, lead times, and other specifications.
Flat-Bed Die Cutting
The flat-bed die cutting process, also known as clam shell die cutting, is one of the most common die cutting processes used in the manufacturing industry. The process involves using a flat-bed press to stamp out a desired shape by pressing a steel ruled die into the material.
The flat-bed die cutting process is a versatile and efficient method of creating components in large quantities. It is commonly used in the manufacturing of products such as packaging, gaskets, spacers and labels.
Preco Automated Die Cutting
Preco automated die cutters use a video optical registration system to ensure that the finished “print to cut” alignment is right every time. The camera system locates targets that have been printed on the press sheets and adjusts the strike of the die to those targets. If the printing moves on the sheet so does the cutting. This process also allows us to purchase fewer cavities in a tool. With the camera registration system, the press will “step through” the sheets with exacting precision. As an example, at JN White, it is very common for us to use a 5-up Preco tool for a 20 up printed sheet saving our customers money on their initial tooling charges.
Digital Die Cutting
Digital die cutting converts material without the use of dies. Instead, they employ computer-controlled lasers, blades, and tool bits to produce cuts, scores, and kiss cuts. This process is suitable for low-shear material converting applications requiring fast lead times and low costs while maintaining high precision.
At JN White our laser-cutting system is precise, cost effective and ideal for every aspect of polycarbonate and acrylic material manufacturing, from prototyping and short-run projects to full production of otherwise hard-tooled programs. Our multiple machines, at our 2 different manufacturing facilities, can cut with extreme precision on polycarbonate materials up to 1MM thick and acrylics as thick at 5MM.
JN White also utilizes a Zund Digital Blade Cutting system that excels at cutting a variety of materials, particularly for short-run projects. We typically recommend and use this method on kiss cut label jobs where the volume warrants digital cutting (no tooling) and the customer wants several parts delivered on a carrier sheet.
Industries that Utilize Precision Cut Components
Die cut components are used in various manufacturing applications, including:
Automotive: Die cut gaskets and seals are commonly used in the automotive industry to prevent leaks and reduce noise and vibration.
JN White implemented an innovative rubber solution engineered specifically for a prominent automotive electronic system companies’ application. The primary purpose of the neoprene gasket is twofold. Firstly, it effectively seals the speaker, providing protection against water and environmental factors. This ensures the longevity and reliability of the audio system, even in challenging conditions.
Moreover, the gasket acts as a remarkable “gap pad,” offering significant benefits to the overall sound quality. By creating a separation between the speaker and the face of the keys, it minimizes any interference that could negatively impact sound clarity. This enhancement guarantees an exceptional auditory experience for users.
Electronics: Die cut components are used in the electronics industry to produce insulators, seals, EMI shielding, spacers and gaskets for electronic devices. They are also used in displays and touchscreens.
JN White created a cutting-edge solution in electronic shielding. With its distinctive tin-coated copper construction and custom-applied mylar insulator on both sides, this shield offers unparalleled protection and performance.
The aluminum shield serves a critical function in the product line by providing essential EMI (Electromagnetic Interference) protection for the PCB (Printed Circuit Board). It’s precisely engineered die cuts in the mylar expose the tin-coated copper, serving as soldering points for efficient grounding of the shield.
The tin coating on the copper ensures optimal conductivity while the custom mylar insulation provides insulation and prevents unwanted electrical contact. The strategic placement of the aluminum shield effectively minimizes the risk of electromagnetic interference, guaranteeing the optimal functionality and performance of the product. It acts as a vital line of defense, safeguarding the delicate electronics from external interference, thereby ensuring their smooth operation.
Medical: Die cut components are used in the medical industry to produce gaskets, seals, and filters for medical devices providing precision, functionality, and reliability in healthcare settings.
JN White developed a cutting-edge solution engineered to improve sound quality in a medical device. This speaker grill support piece is crafted from .020″ thick polycarbonate and features 3M468 adhesive on both sides. With laser-cut precision, it addresses a common challenge encountered in audio systems.
When a graphic overlay with a similar pattern is placed over a speaker, vibrations from the speaker can cause interference and compromise sound quality. Our polycarbonate support piece was specifically engineered to address this issue. By placing it beneath the graphic overlay, it effectively dampens vibrations, resulting in a clearer and more pristine sound output. The meticulous engineering and high-quality materials ensure exceptional performance and durability.
Overall, precision cut components are a highly customizable and versatile process that can produce a wide range of shapes and designs. With its different capabilities and types of die cutting processes, it can be applied to a variety of materials and industries.
Precision cut components play a significant role in various industries such as automotive, electronics, and medical. These components offer versatile solutions for vibration damping, EMI shielding, electrical insulation, and more. With the utilization of advanced cutting systems like flat-bed die cutting, Preco automated die cutting, and digital die cutting, JN White provides tailored solutions for specific applications. By leveraging our expertise in durable materials, JN White delivers high-precision components that enhance product performance and durability in diverse industries. With our commitment to innovation and advanced manufacturing techniques, JN White continues to provide cutting-edge solutions for precision cut components in the ever-evolving manufacturing landscape.
More from Ken
The JN White Memorial Scholarship Committee is proud to announce that Tess McLaughlin has been selected as the 2025 recipient of the JN White Memorial Scholarship. Tess embodies the spirit of leadership, academic excellence, and community service that this scholarship…
We’re excited to share that JN White has been recognized in the In the Lead: Best Family-Owned Businesses in Rochester program, which celebrates outstanding family-owned companies making significant contributions to our region’s economy and community. Founded in 1960 by James…
In today’s rapidly evolving technological environment, the need for innovative and dependable membrane switch prototypes is continuously increasing. As a leading membrane switch manufacturer, JN White excels in crafting custom membrane switch prototypes that not only meet your specific design…