Understanding Conductive Inks
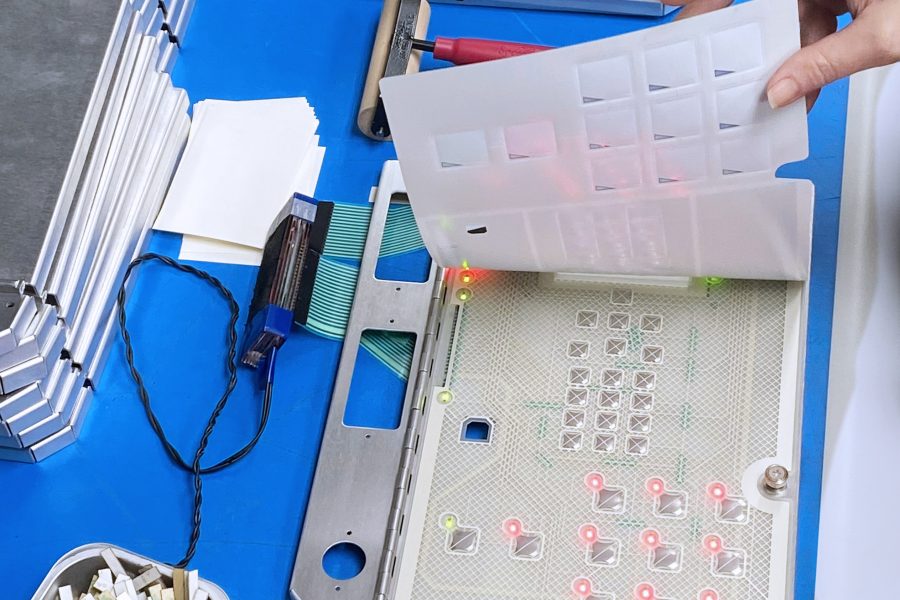
This blog post is dedicated to the intriguing world of conductive inks. We will dive into the details of their unique properties, applications, and the materials suitable for their application. If you are intrigued by technological advancements or work with conductive inks, this post is designed for you.
Conductive inks, as the name suggests, are a type of ink that can conduct electricity. They find their purpose in a broad spectrum of applications ranging from printed electronics to solar cells, heaters and touchscreens. These inks encapsulate conductive materials like silver, copper, or carbon which are responsible for their conductive properties.
Ready to learn more about the surfaces where you can apply conductive inks? Keen to delve deeper into the properties that make conductive inks so versatile? Join us as we explore these areas in the following sections.
Exploring the Core of Conductive Inks
Conductive inks are a unique category of materials that are indispensable in several industries. These inks are specifically formulated to conduct electricity, making them invaluable for a broad range of applications.
Conductive inks consist of conductive particles dispersed in a liquid medium, typically a polymer or solvent-based solution. These conductive particles could be composed of a variety of materials like silver, copper, carbon, or even graphene. These particles bestow the ink with its electrical conductivity.
There is a variety of conductive inks available, each with its unique properties and uses. Some common types include:
- Silver-based conductive inks: These inks are extensively used due to silver’s high electrical conductivity and stability. They are predominantly used in applications such as printed electronics, RFID tags, and touchscreens.
- Copper-based conductive inks: Copper is another highly conductive material used in inks. These inks are frequently used in flexible electronics, solar cells, and antennas.
- Carbon-based conductive inks: Inks containing carbon particles are known for their adaptability and cost-effectiveness. They find uses in sensors, printed heaters, and electromagnetic shielding.
- Silver / Silver Chloride inks: Typically used for printing disposable EKG and EEG electrodes, defibrillator pads and medical sensors.
The applications of conductive inks are vast and continue to grow. They have brought about revolutions in industries like electronics, automotive, healthcare, and energy. Some common applications include:
- Printed circuit boards (PCBs): Conductive inks are used to create conductive traces on PCBs, enabling the flow of electrical signals between components.
- Flexible and wearable electronics: Conductive inks facilitate the fabrication of flexible and stretchable electronic devices like smart clothing, sensors, and displays.
- Solar cells: Specific types of conductive inks are used to create conductive layers in solar cells, aiding the conversion of sunlight into electricity.
- RFID tags: Conductive inks are used to print the antennas and circuits required for RFID technology, enabling wireless communication and identification.
At JN White, we utilize high-quality conductive inks. Our conductive inks are formulated to provide excellent conductivity, durability, and compatibility with various substrates. Whether you require inks for printed electronics, membrane switches, or any other application, our team is equipped to provide tailored solutions to meet your specific requirements.
Suitable Substrates for Conductive Inks
When it comes to applying conductive inks, several substrates can be considered. These substrates serve as a base for the ink, ensuring optimal conductivity. Let’s explore some of the common materials where conductive inks can be applied:
Suitable Substrates for Conductive Ink Application:
- Paper: Conductive inks can be applied to paper, making it a suitable choice for printed electronics, RFID tags, and flexible circuits. The flexibility and cost-effectiveness of paper make it a popular substrate for various applications.
- Glass: Conductive inks can be used on glass substrates, enabling the creation of transparent conductive films. This is particularly useful for applications such as touchscreens, OLED displays, and solar cells.
- Plastic: Conductive inks can be applied to plastic substrates, offering flexibility and durability. Plastic materials like PET and PVC are commonly used for applications such as smart packaging, wearable devices, and automotive electronics.
- Textiles: Conductive inks can be used on textiles, transforming them into functional smart fabrics. This opens up possibilities for wearable technology, e-textiles, and interactive garments.
- TPU (Thermoplastic Polyurethane): TPU is a type of thermoplastic elastomer. It is another versatile substrate for conductive ink application. Its thermoplastic nature allows for flexibility and resilience, making it suitable for a range of applications. TPU can be employed in the development of flexible circuits, smart textiles, and various electronic components.
Considerations for Different Materials:
While conductive inks can be applied to a range of materials, it’s important to consider the specific properties and characteristics of each substrate. Factors such as surface roughness, porosity, and compatibility with the ink formulation should be considered for optimal performance.
Compatibility with Various Surfaces:
Conductive inks are designed to be compatible with various surfaces, ensuring good adhesion and conductivity. Whether it’s a smooth glass surface or a textured textile, conductive inks are formulated to provide reliable performance across different substrates. Ink manufacturers are constantly developing formulations that will adhere to new and exciting substrates.
Key Characteristics of Conductive Inks
Conductive inks possess several key characteristics that determine their performance and applications. Understanding these characteristics can help you make informed decisions and find the right conductive ink for your specific needs. Let’s take a closer look at three important characteristics: electrical conductivity and resistivity, viscosity and rheology, and adhesion and durability.
Electrical Conductivity and Resistivity:
One of the primary functions of conductive inks is to provide a pathway for electrical current. The electrical conductivity of an ink determines how effectively it can conduct electricity. Conductive inks with high electrical conductivity offer low resistance, allowing for efficient current flow. On the other hand, resistivity measures the material’s resistance to conduct electricity. Conductive inks with low resistivity are more desirable as they minimize energy loss and heat generation.
Viscosity and Rheology:
Viscosity refers to the thickness and flow behavior of a conductive ink. It plays a crucial role in the printing process, as it affects ink deposition and uniformity. Inks with high viscosity may require additional processing or modifications to achieve the desired results. Rheology, on the other hand, studies the flow and deformation of materials under applied stress. Understanding the rheological properties of conductive inks helps determine their suitability for specific printing techniques and equipment.
Adhesion and Durability:
Adhesion and durability are vital considerations for any application involving conductive inks. Adhesion refers to the ink’s ability to bond to the substrate or surface it is applied to. Good adhesion ensures reliable and long-lasting performance. Durability encompasses the ink’s resistance to environmental factors such as moisture, temperature changes, and mechanical stress. Conductive inks with excellent adhesion and durability ensure reliable conductivity over an extended period.
More from Ken
In today’s rapidly evolving technological environment, the need for innovative and dependable membrane switch prototypes is continuously increasing. As a leading membrane switch manufacturer, JN White excels in crafting custom membrane switch prototypes that not only meet your specific design…
Projected Capacitive (PCAP) touch technology has revolutionized modern touchscreens, providing highly responsive, durable, and intuitive user experiences. From smartphones to industrial control panels, PCAP touchscreens are now the gold standard for applications requiring precision and reliability. At JN White, we…
Understanding the Importance of ESD Shielding Electrostatic Discharge (ESD) is a critical concern in electronic device design, particularly for sensitive components like membrane switches. Without proper ESD protection, these switches can suffer from performance issues, reduced lifespan, or even total failure….