10 Ways to Get the Most from Rapid Prototyping in Manufacturing
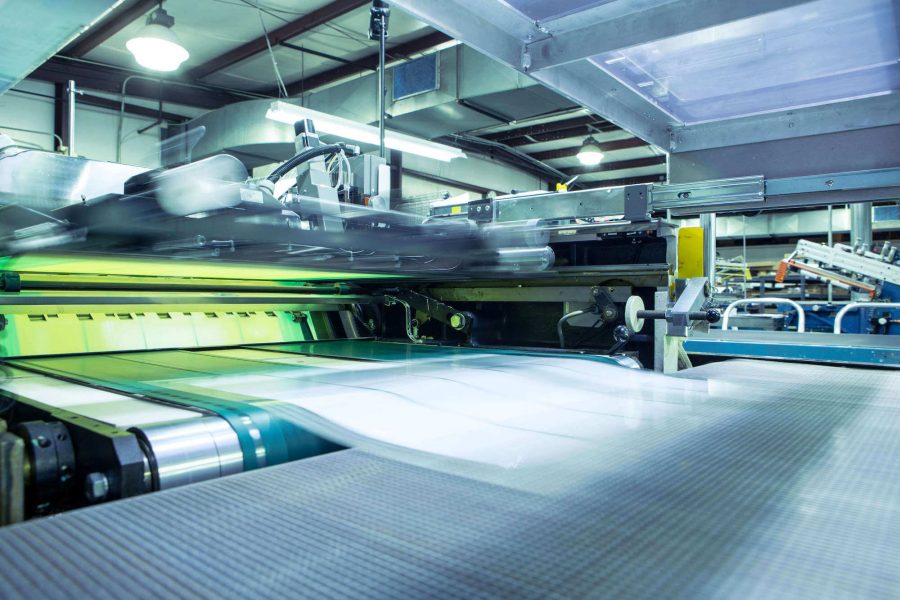
Rapid prototyping improves the manufacturing process, allowing for better iteration and testing during the early stages of product development. At JN White®, we’ve used 3D modeling to revolutionize the rapid prototyping of complex user interfaces, membrane switches, graphic overlays, and labels.
This is important progress since prototyping is essential in all types of manufacturing. Still, too many companies don’t want to spend time and money on prototyping. In some cases, this can lead to serious problems during production — problems you want to avoid. With that in mind, I’d like to share the top 10 ways a partnership with JN White® can help you avoid the most common pitfalls during the early stages of production.
1 – Choose the Right Reasons for Rapid Prototyping
Rapid prototyping can solve a lot of design issues, but it’s not right for everything. You can easily exceed your budget creating large, simple parts and parts that don’t require tight tolerances. This can take away funding from other critical parts of production. “Remember that not only are some technologies more expensive, but that the need for post-processing can also drive costs upward,” says Machine Design. JN White® can help you determine whether or not rapid prototyping is the right next step in your design process (or if other techniques would be more efficient).
2 – Choose the Right Orientation
Orientation during prototyping will determine the success of your design when it reaches production. If you don’t keep design rules in mind early on, you will waste time and resources when you’re forced to backtrack later. Set up a successful framework to define rules, principles, and process characteristics that will improve long-term precision and success.
3 – Choose the Right Tools and Materials
One set of materials and machines does not fit all prototyping scenarios. The materials and technologies you choose will impact development stages later. But you can select tools and resources that maximize success rates for multiple prototyping scenarios. At JN White®, we use only fully functional parts and components in our four-step rapid prototyping process for this purpose.
4 – Communicate Effectively
When designers and prototypers don’t communicate effectively, they are setting themselves up for failure — even with the most exceptional ideas, tools, and materials. It’s especially important that these parties identify the full product scope and potential risks — well before prototyping begins — so they can select the right resources and methodologies for the job.
5 – Optimize the Assembly Process
Assembly problems can quickly derail the later stages of production. Ensure rapid prototyping factors in the risks you established during the planning stages of your prototyping effort in terms of the materials you select and the tolerances you prioritize. If your materials fail or you don’t allow for tolerance variances, you and your team will be kicking yourselves later.
6 – Take Advantage of the Full Prototyping Process
Don’t expect your first iteration to be perfect. Take a deliberate approach to using the entire prototyping process to your advantage. Anticipate needing multiple attempts to determine an ideal design so you can get the most out of each step of the process.
7 – Don’t Overdo It
Still, you want to avoid over-producing in an impossible quest for perfection. Plus, novice designers often waste time and resources making multiple assemblies but failing to maximize the value of those efforts each time. You may save time and money by making components and proving them individually before building a larger device as well.
8 – Keep the Final Product in Mind
Ensure you have the final product’s intended use in mind throughout the prototyping process. For example, prototypers can fail to factor in the necessity of mass production later, complicating its potential with too much complexity. Keep factors like aesthetics, production costs, and usability in mind as well.
9 – Know Your End User
Keep the end customer front of mind early on during prototyping and design. At each stage of the process, envision how your ideal user will perceive the end product and use it to his or her benefit. You may identify potential pitfalls and save time later on errors you otherwise would not have noticed.
10 – Choose the Right Rapid Prototyping Partner
At JN White®, we offer custom rapid prototyping of membrane switches for some of the most challenging and high-stakes manufacturing needs today. As natural problem solvers, we keep your unique challenges and manufacturing goals in mind. Get a free quote for your next project and see why 30 years of getting this right has paid off for our customers.
More from Ken
In today’s rapidly evolving technological environment, the need for innovative and dependable membrane switch prototypes is continuously increasing. As a leading membrane switch manufacturer, JN White excels in crafting custom membrane switch prototypes that not only meet your specific design…
In today’s rapidly evolving landscape of product identification and regulation, ensuring traceability and compliance is paramount for manufacturers across various industries. One crucial aspect of this is the implementation of Unique Device Identification (UDI) barcode labels for products. Among the…
Although commonly referred to as die cuts, die cutting is just one process utilized to create precision cut components. Die cutting is a versatile and widely used fabrication process that involves specialized machines and tools to convert stock material into…