Ensuring Traceability and Compliance with UDI Barcode Labels
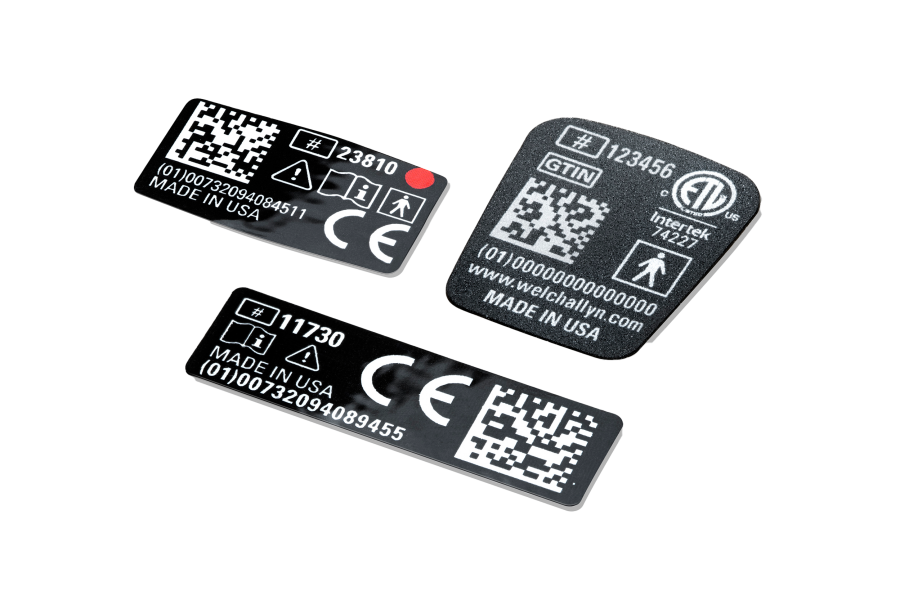
In today’s rapidly evolving landscape of product identification and regulation, ensuring traceability and compliance is paramount for manufacturers across various industries. One crucial aspect of this is the implementation of Unique Device Identification (UDI) barcode labels for products. Among the pioneers in this field is JN White, a company dedicated to providing cutting-edge solutions for labeling needs. Let’s delve into the significance of UDI barcode labels and how JN White is leading the way in this crucial aspect of modern manufacturing.
Understanding UDI Barcode Labels
UDI is a system used to adequately identify medical devices throughout their distribution and use. It involves assigning a unique identifier to each medical device model and entering key device information into a central database maintained by the FDA (Food and Drug Administration) in the United States. This initiative aims to enhance patient safety, streamline recalls, and improve overall supply chain efficiency.
These labels contain crucial information such as the device identifier, production identifier, and if applicable, expiration date and batch/lot number. By scanning these barcodes, stakeholders can access essential details about the device, facilitating accurate tracking, and ensuring regulatory compliance.
The Importance of UDI Barcode Labels
- Enhanced Patient Safety: UDI barcode labels enable healthcare providers to accurately identify and track medical devices used in patient care. This ensures that the right device is used for the right patient, reducing the risk of errors and adverse events.
- Streamlined Recalls: In the event of a product recall or safety alert, UDI barcode labels enable swift and precise identification of affected devices. This facilitates targeted recalls, minimizing disruption to healthcare operations and reducing potential harm to patients.
- Improved Supply Chain Efficiency: UDI barcode labels enhance visibility and traceability throughout the supply chain, from manufacturing to distribution and beyond. Manufacturers and distributors can accurately track the movement of devices, optimize inventory management, and respond promptly to market demand.
- Regulatory Compliance: Compliance with UDI regulations is mandatory for manufacturers of medical devices in many countries, including the United States and the European Union. Failure to comply can result in regulatory penalties, market access restrictions, and reputational damage. Utilizing UDI barcode labels ensures adherence to these regulations, safeguarding market access and brand integrity.
Grading for Class II Medical Device Barcodes
For Class II medical devices, this involves more than just printing a readable barcode; it requires that the barcodes be graded to specific criteria to ensure they are scannable and reliable throughout the device’s lifecycle.
At JN White we have advanced grading technology, this evaluates the barcode’s print quality and scannability against the FDA’s criteria. This process involves rigorous testing to ensure that each barcode achieves the necessary grade for compliance. By doing so, we help our clients avoid potential regulatory issues and ensure their products are ready for the market.
The grading process involves checking various aspects of the barcode, such as contrast, modulation, defects, decodability, and more. This comprehensive testing ensures that the barcode will be readable under various conditions and by different scanning devices, which is crucial for maintaining traceability and compliance.
We are able to provide reports documenting the grading results for each batch of UDI barcode labels. This documentation is essential for FDA audits and helps manufacturers demonstrate compliance with regulatory standards.
JN White: Your Partner in UDI Barcode Labeling Solutions
With over 60 years of experience in the labeling industry, JN White has established itself as a trusted partner for companies seeking innovative labeling solutions. Leveraging state-of-the-art technologies and a commitment to quality and customer satisfaction, JN White offers a comprehensive range of UDI barcode labeling solutions tailored to meet the unique needs of medical device manufacturers.
From durable barcode labels suitable for harsh environments to variable data printing capabilities for dynamic information such as lot numbers and expiration dates, JN White provides customizable solutions designed to ensure compliance and enhance operational efficiency.
Our team of experienced professionals offers guidance and support throughout the implementation process, helping clients navigate complex regulatory requirements and achieve seamless integration of UDI barcode labeling systems into their operations. We have the capability to grade the barcodes to FDA standards and provide comprehensive documentation to support compliance.
UDI barcode labels play a crucial role in ensuring traceability, compliance, and patient safety in the medical device industry. By partnering with JN White, manufacturers can access cutting-edge labeling solutions tailored to their specific needs, enabling them to meet regulatory requirements, enhance operational efficiency, and deliver safe and reliable products to the market.
Question to ask yourself when looking for a manufacturing partner:
Has the label manufacturer worked with an FDA-accredited issuing agency?
- Ideally, your manufacturing partner should understand how to help you work with an FDA-accredited issuing agency (GS1, ICCBBA, or the Health Industry Business Communications Council (HIBCC)).
Does the label manufacturer know the needs of your supply chain?
- A good labeling partner can help you determine what information you need to put in your UDI barcode label, depending on the needs of your supply chain.
Does the label manufacturer have the capabilities to manage, print, and check both 2D and FDA-accredited matrix barcodes?
- These capabilities include variable data printing, the appropriate barcode encoding software, and a documented process to test the labels. In the case of an FDA audit, you need to be able to prove that the labels have graded out to the desired level. This must be supported by the appropriate records and documentation.
Does the label manufacturer grasp the environmental context in which your label will reside?
- Good manufacturers choose substrates, adhesives, sizes, colors, overlaminates and other elements based on environment-specific issues that can affect your label, including durability, temperature and humidity parameters, chemical resistance, abrasion resistance, legibility, visual appeal, etc.
Contact JN White today to learn more about their UDI barcode labeling solutions.
More from Ken
Biosensors stand at the cutting edge of precision detection technology, integrating biological components with electronic systems to deliver fast and accurate measurements of various analytes. As the need for advanced diagnostic tools and monitoring systems escalates, biosensors are set to…
In today’s rapidly evolving technological environment, the need for innovative and dependable membrane switch prototypes is continuously increasing. As a leading membrane switch manufacturer, JN White excels in crafting custom membrane switch prototypes that not only meet your specific design…
In an age where electronic devices are at the core of nearly every industry, protecting sensitive equipment from electromagnetic interference (EMI) and radio frequency interference (RFI) is crucial. One of the most effective solutions for shielding electronics from these disruptive…