Shining Some Light on Your Backlighting Options
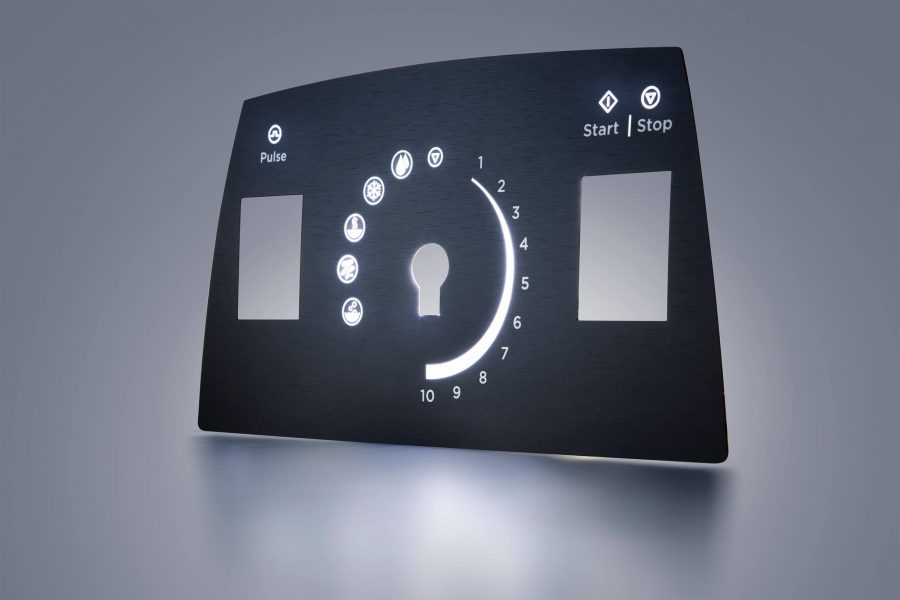
Although they create great end-user experiences, backlighting technologies can be a real challenge for engineers and manufacturers. In our day-to-day work, we find ourselves executing a variety of different options in the membrane switch assemblies we produce for our customers.
LEDs (Light Emitting Diodes)
Perhaps the simplest, and most common, technique involves LEDs (light emitting diodes). These low-cost, low-power, highly reliable light sources come in a range of colors and intensities, so there’s a great deal of freedom from a design perspective. Circuit cards with embossed LEDs can be layered under translucent graphic layers, or side-firing LEDs can be strategically placed around the buttons of a switch assembly.
The problem is that these are single-point light sources.
You need to know how to smooth out the “hot spot” so you get a more user-friendly, visually pleasing result. This typically involves incorporating diffusing layers into the assembly, which of course adds costs and time to the manufacturing process.
Electroluminescent (EL) Lamps
Another choice is electroluminescent (EL) lamps. These produce light by charging phosphors with AC/DC current – a highly efficient, solid-state method for converting electricity to light. We usually implement them with an EL panel behind a graphic overlay (which works well because of the minimal heat throw of these light sources). People really love the smooth, even look of EL lamps, and they are extremely thin, so they provide a lot of flexibility when designing backlit assemblies.
However, the challenge with EL lamps is the alternating current source.
Typically, this is an inverter, and these can be very, very noisy. So, while EL lamps are a great option, many of our customers don’t want to support them electronically. Where this isn’t a factor (in equipment and devices that already feature inverters for other purposes), EL lamps are a wonderful choice. For example, a prominent figure in the musical instrument sector relies heavily on this technology due to its capacity to yield top-tier outcomes, aligning with the desired brand image and the demanding performance settings of their products.
Fiber Optics
An old-school backlighting technology that is still in use today is fiber optics.
With this approach, an LED shines through the optical fiber, allowing you to light very specific parts of a membrane switch. Customers really love this – very cool temperatures, only one LED for a broad area, low power requirements. Fiber optics check all the boxes. As with any technology, though, there are drawbacks. For fiber optics, it is the bulky pigtail that is formed when multiple optical fibers are brought together at the LED. In an era of miniaturization, that’s a challenge.
And that brings us to new-school fiber optics.
We’ve used this approach with a major consumer appliance brand for their high-end blenders. Instead of single strands of fiber optics brought together in a pigtail, their products rely on a woven fiber optic pad. We cut holes in that pad and then light it with a side-firing LED. This removes the pig-tail issue, which is great. It is compact, controlled, and low power consumption. It’s a great technology, but extremely expensive to produce. Imagine the precision looms required to make a woven fiber optic!
Light Guide Layer (LGL)
So now, the industry has come up with Light Guide Layer, or LGL, technology. With LGL, a light-diffusing plastic material is being used in place of woven fiber optic pads. It’s a much more affordable solution, which makes it great for high-volume, low-cost situations. The only issue is that they require more LEDs to achieve the same light effects, which means more components, more electronics, etc. Therefore, they aren’t ideal for every application.
As you can see, there are many options for handling your backlighting objectives. The key is to work with an assembly manufacturer who understands the pros and cons of each approach. Also, they can give you the right advice when you are making these critical design decisions.
By: Ken Boss, Vice President of Sales at JN White®, a leading ITAR certified manufacturer. He is an expert in the production of graphic overlays, membrane switches, user interfaces, control panels and custom labels. JN White’s Quality System is certified as being in conformity with ISO 9001:2015 by Intertek.
More from Ken
Biosensors stand at the cutting edge of precision detection technology, integrating biological components with electronic systems to deliver fast and accurate measurements of various analytes. As the need for advanced diagnostic tools and monitoring systems escalates, biosensors are set to…
In today’s rapidly evolving technological environment, the need for innovative and dependable membrane switch prototypes is continuously increasing. As a leading membrane switch manufacturer, JN White excels in crafting custom membrane switch prototypes that not only meet your specific design…
Projected Capacitive (PCAP) touch technology has revolutionized modern touchscreens, providing highly responsive, durable, and intuitive user experiences. From smartphones to industrial control panels, PCAP touchscreens are now the gold standard for applications requiring precision and reliability. At JN White, we…