Signs You Might Need Copper Flex Circuitry
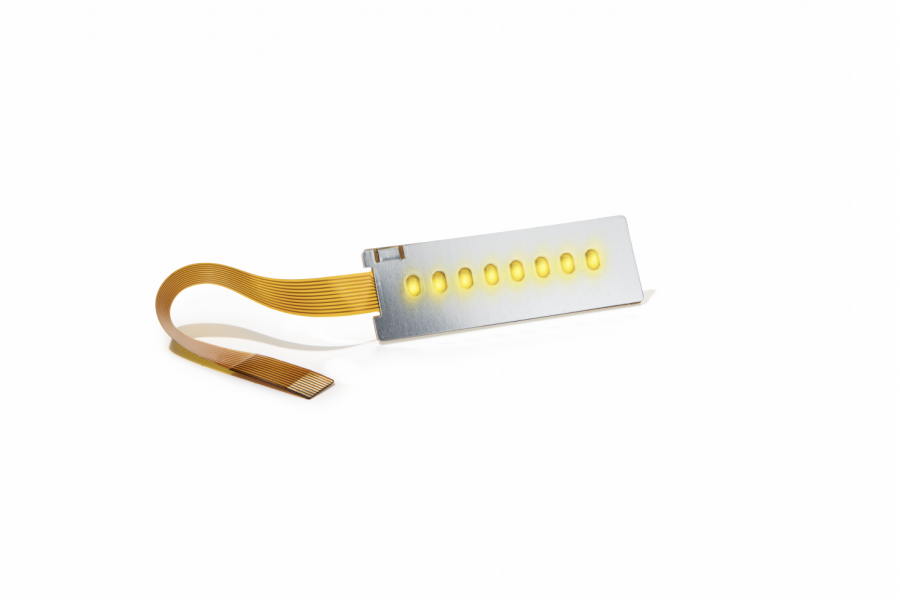
Flexible circuits are an essential tool in the design of compact electronics, like consumer appliances or medical device products. In our business, they are typically employed on ribbon cables that link membrane switches (and other control interfaces) to underlying circuit boards and functional electronics.
Usability and convenience are top priorities in these applications, and the interconnections between components need to conform to very demanding design parameters. Which raises the question – copper flex or silver flex circuits?
While they are similar, the differences can be stark. Silver flex is usually screen-printed onto the underlying ribbon cable. Very simple and inexpensive. Easy to design. Easy to manufacture. Copper flex, on the other hand, involves the lamination of copper to the underlying substrate, which is then etched to leave the desired conductive traces. This is a more rigorous, more demanding process.
Each certainly has its place. At JN White®, we like to work with our customers’ engineers to figure out just what the right solution will be. In my experience, there are three key drivers in a decision to choose copper flex over silver flex circuitry.
Reason 1 – Durability
The biggest drawback with screen-printed silver is that it will crack upon bending and creasing, which will break the circuit. Copper flex holds up in these situations.
So this means the choice depends on your design, and what exactly is happening with that ribbon cable.
For most of the products we manufacture, the tail of the ribbon cable threads from an interface and into the unit, usually connecting to a circuit board. If it is a complex path, the ribbon cable needs to be more durable. We’re going to be bending, folding, and putting all kinds of other stresses on it. That means copper flex is the right choice. This is especially true with more compact products.
If it is a straight path, with little or no interference, then silver flex will work just fine.
Reason 2 – Components
Here’s where the substrate comes into play.
The base material of copper flex circuits is polyimide. This a very high-temperature substrate, so we can solder components to it – LEDs, resistors, light sensors, etc. This gives engineers a lot more freedom of design.
With silver flex, you use a conductive epoxy, which just isn’t going to hold up to the more robust solder required to attach components. And when you have a situation where you can attach these additional pieces, the work needs to be done by hand to accommodate the fragility of the silver flex circuit.
Copper flex is completely different. If you have multiple pick-and-place reflow components, you can automate the application of solder and parts (as we would do with PCBAs). Copper flex is much more efficient in that it allows you to leverage these advanced automated placing methods.
Reason 3 – Precision
This factor relates to the space between the traces (or conductors) at the end of the ribbon cable. Too far and you are working with large, bulky connectors. Too close, and you’ll short your circuit. So the level of precision you need from the “tail” of your circuit is critical.
With silver, the smallest we can get to is a 1mm pitch. Copper flex gives us the ability to go as small as 0.5mm – a 2X difference, which can make all the difference.
This becomes a much bigger deal as electronics get smaller and smaller. Everything needs to shrink, including the connectors on the circuit boards. And this is where copper flex can really shine. There is much more precision and control.
While the challenges and costs associated with copper flex circuits can seem daunting, they can absolutely carry the day when they are matched up with the right requirements.
Click here to see how we solved one customer’s challenge with copper flex.
By: Ken Boss, Vice President of Sales at JN White®. He is an expert in the production of graphic overlays, membrane switches, user interfaces, control panels and custom labels. JN White is ITAR Certified and its Quality System is certified as being in conformity with ISO 9001:2015 by Intertek.
More from Ken
Biosensors stand at the cutting edge of precision detection technology, integrating biological components with electronic systems to deliver fast and accurate measurements of various analytes. As the need for advanced diagnostic tools and monitoring systems escalates, biosensors are set to…
In today’s rapidly evolving technological environment, the need for innovative and dependable membrane switch prototypes is continuously increasing. As a leading membrane switch manufacturer, JN White excels in crafting custom membrane switch prototypes that not only meet your specific design…
Projected Capacitive (PCAP) touch technology has revolutionized modern touchscreens, providing highly responsive, durable, and intuitive user experiences. From smartphones to industrial control panels, PCAP touchscreens are now the gold standard for applications requiring precision and reliability. At JN White, we…