Serving the Needs of Healthcare Professionals
At JN White, we understand the unique demands of the medical industry. From small startups to large manufacturers, our comprehensive range of solutions—including flexible heaters, user interface assemblies, graphic overlays, and labels—ensures your medical devices meet both performance and regulatory standards. We are committed to helping you deliver safe, reliable, and effective solutions that make a difference in patient care.
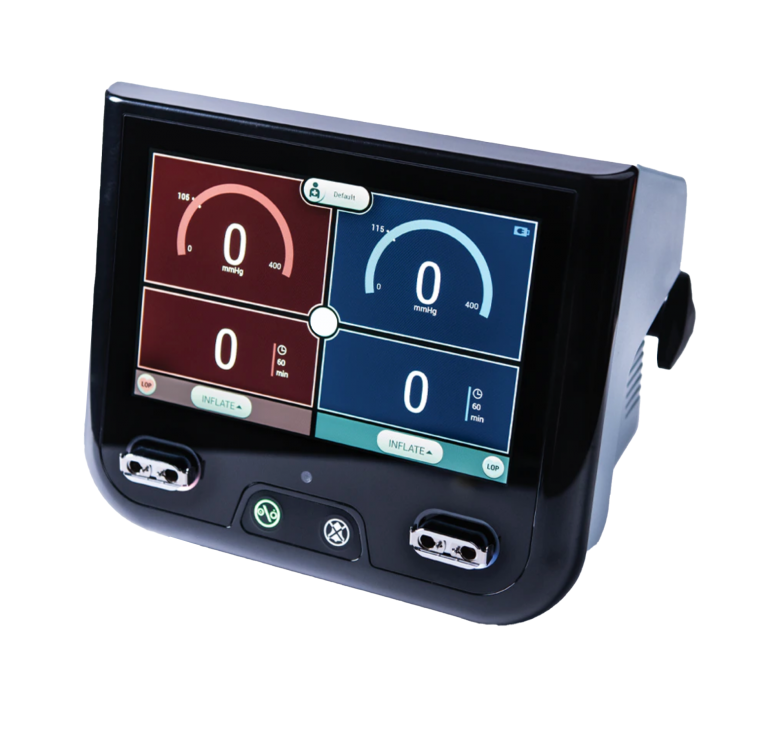
Medical Device User Interface Capabilities
Durable Materials
In healthcare, hygiene and cleanliness are critical. Our medical user interfaces are built with materials specifically selected to endure frequent cleaning with harsh chemicals, ensuring that your devices remain safe, effective, and operational over time.
-
Chemical Resistance: We use materials that resist degradation from commonly used medical-grade cleaning agents, ensuring long-term durability.
-
Antimicrobial Properties: To help minimize the spread of infections, we integrate antimicrobial treatments into our materials, reducing bacterial growth on key surfaces and improving patient safety.
Standard Controls
To improve usability, we’ve found it preferable to stick with standard or previously approved designs. By presenting controls that medical personnel are already familiar with, we can help them avoid potentially dangerous operational mistakes. For new products and new user interface designs, we typically develop fully functioning prototypes for usability testing, allowing engineers to assess the true impact of the control units they are proposing.
Tactile Feedback for Precision and Confidence
For medical professionals, every interaction with a device must provide clear, responsive feedback. Our custom-designed user interfaces incorporate advanced tactile features that ensure users feel confident and accurate in their interactions.
-
Responsive Keypads: Buttons and switches are designed to deliver a satisfying, responsive tactile feedback, reducing user error and increasing efficiency.
-
Touchscreen Sensitivity: We engineer touchscreens that react instantly to user commands, even under gloved hands, providing a smooth and reliable experience for healthcare providers.
Seamless User Experience
Medical devices are complex, but the user experience should be seamless. Whether it’s a touch panel for a diagnostic machine, a control interface for a therapeutic device, or a simple yet effective display for monitoring systems, we engineer medical user interfaces with a focus on ease of use, accuracy, and durability. Our medical UI assemblies include:
-
Touchscreens and Keypads: Custom-designed to meet specific needs while providing responsive interaction for healthcare professionals.
-
Graphic Overlays: Clear, intuitive, and durable overlays that simplify device operation, ensuring users can access critical functions quickly and accurately.
-
User-Centered Design: We focus on creating user interfaces that enhance workflow and minimize user error in high-pressure medical environments.
Visual Impact and Clarity
Clear visual communication is essential in medical devices to ensure quick, accurate decision-making. Our graphic overlays and touchscreen designs focus on delivering high-contrast, easily legible displays that enhance usability.
-
High-Visibility Graphics: Vibrant, high-contrast graphics are easily readable in various lighting conditions, ensuring users can operate devices quickly and accurately.
-
Customizable Displays: Whether it’s for control panels, diagnostic tools, or therapeutic devices, we work with you to create overlays that align with your device’s functions and improve user comprehension.
User-Centered Design for Healthcare Excellence
Medical devices require user interfaces that are not only functional but also intuitive. We prioritize designing interfaces that simplify complex tasks and ensure users—whether they’re healthcare providers or patients—can interact with the device easily and efficiently.
-
Ergonomic Layouts: Controls and displays are strategically placed to provide intuitive navigation and ease of use, reducing the risk of mistakes in high-pressure environments.
-
Accessibility Features: We design with accessibility in mind, creating interfaces that are usable by people of all skill levels and abilities, making medical devices more inclusive and user-friendly.
Manufacturing Quality
By their very nature, medical devices are operating in potentially life-impacting situations. This means they must be 100% reliable. At just 99.9% reliability, 20,000 incorrect drug prescriptions will be written each year and 291 pacemaker operations will be performed incorrectly.* We have a lot of experience with this requirement; we specify quality components, follow strict process control procedures, perform rigorous testing, and adhere to the highest manufacturing standards to ensure the membrane switch assemblies in your devices deliver that high level of reliability this market demands.
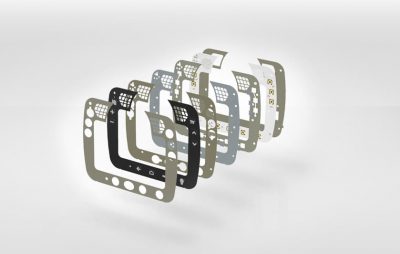
Turn Your Concept Into A Prototype
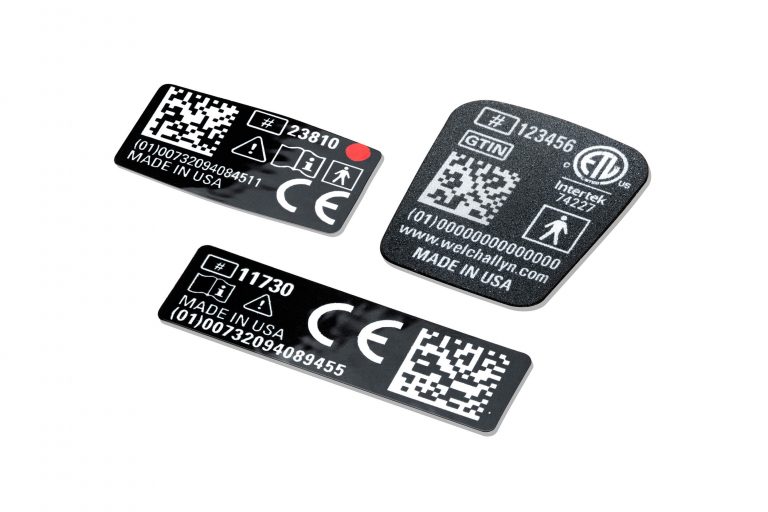
FDA Labeling for Medical Devices
Medical device labels must hold up, and so we use superior substrates and processes to make sure they do just that. We’re a leading label and component manufacturer with a Quality System that is certified as being in conformity with ISO 9001:2015 by Intertek, so you can rest assured our products are worthy of yours. We also have extensive knowledge and experience producing FDA-compliant Unique Device Identification (UDI) labels.
Starting in 2013, the US Food & Drug Administration (FDA), the European Commission (CE), and other regulating bodies established new labeling requirements for medical devices. These are the Unique Device Identification, or UDI, requirements.
The goal is to increase patient safety, increase supply chain efficiencies, and improve the traceability of medical devices. These regulations were phased in over time, with all three levels of medical devices – Class III, Class II, and Class I – now in place.
As with many government regulations, the onus is on manufacturers of medical devices to ensure compliance. As one customer told us, “we don’t want to be in the label compliance business, but now we have to be – so help us make it as streamlined and painless as possible.”
At JN White®, we work closely with our customers’ engineers to produce and test combinations of digitally printed labels using sub-surface printing, top surface printing, clear varnishes, clear overlaminates, and other techniques. We then perform the testing necessary to determine which material and design combination grades out the best versus the product requirements. All of this is documented appropriately so that you can go into the accredited agency’s portal and register these parts more quickly and easily since all the information is organized for you.
Working with experts is imperative in this new world of UDI labeling. If you are just starting, we can help you learn more about it. Understand the codes, make sense of the regulations, and do it right.
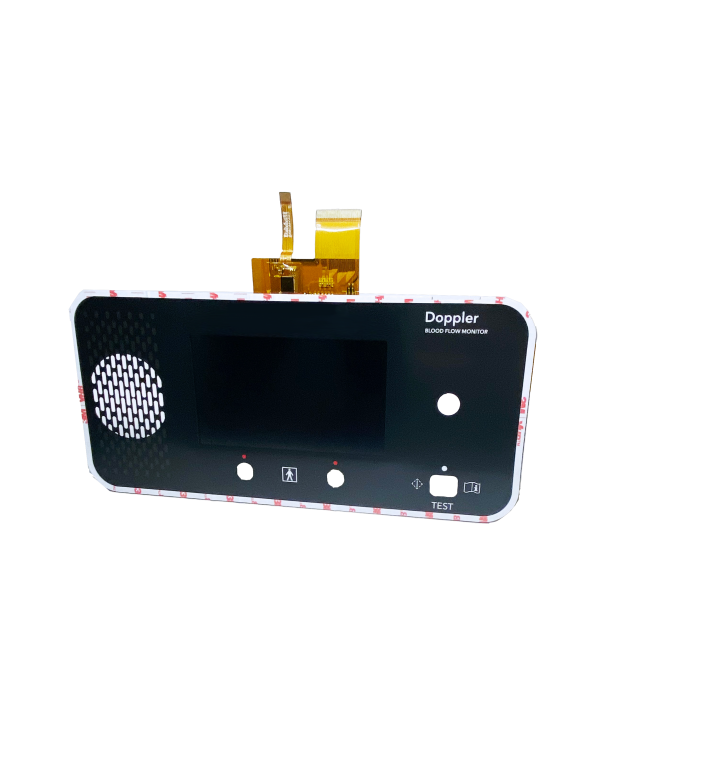
Why Choose JN White for Medical Device Solutions?
-
Precision Engineering: Whether you’re designing user interface assemblies, flexible heaters, or graphic overlays, we collaborate with you to deliver custom solutions that meet your exact specifications and regulatory requirements, ensuring the highest level of performance.
-
Compliance and Safety: Our medical products are rigorously tested and designed to meet the highest industry standards, including ISO and UL certifications. We ensure every component is built for safety and compliance, helping you navigate the complexities of FDA approval and regulatory documentation.
-
Durability and Reliability: From flexible heaters built to withstand the demands of medical environments to durable labels that enhance user experience, our solutions are designed for longevity and consistent performance in critical applications.
-
Collaborative Innovation: We work alongside you every step of the way to develop products that improve patient care, streamline device functionality, and push the boundaries of medical device technology.
See Our Work in the Medical Space
DURABLE MEDICAL CUSTOM MEMBRANE SWITCH
A medical device manufacturer was experiencing durability issues and failures with an important custom membrane switch in the controller of a sophisticated surgical device. The JN White® team applied their extensive experience in medical device design to develop a custom membrane keypad that met all necessary requirements.
UDI LABEL CASE STUDY
A long-term medical device customer needed to transition the labeling on products to new UDI labels that met specific FDA requirements. The deadline for the transition was quickly approaching, so they reached out to JN White® to help them develop and execute the transition to the new labels in a timeline manner.